When temperatures soar in Tulsa, the comfort provided by a functioning air conditioning (AC) system becomes essential for homes and businesses alike. However, as with any mechanical system, air conditioners can experience wear and tear, often requiring repairs to components such as the AC compressor. The compressor plays a pivotal role in the refrigeration cycle, acting as the heart of the air conditioning system by compressing refrigerant and enabling heat exchange. Given its significance, repairing or replacing an AC compressor requires expertise and a keen understanding of safety protocols.
Repairing an AC compressor can be a complex and potentially hazardous task. The job involves handling refrigerants, which are substances that can be harmful if not managed properly, as well as working with high-voltage electrical components. In Tulsa, where the climate can lead to increased demand for air conditioning services, it is crucial for technicians and DIY enthusiasts alike to prioritize safety. Understanding the right safety precautions not only protects the individual working on the unit but also ensures the integrity of the air conditioning system and the surrounding environment.
This article will delve into the essential safety precautions that should be taken when repairing an AC compressor in Tulsa. From understanding the risks associated with refrigerants and electrical components to the importance of using proper personal protective equipment (PPE) and following specific procedures, these guidelines are designed to promote safety and efficiency. Whether you are a seasoned technician or a homeowner attempting repairs, being informed about safety measures is paramount in preventing accidents and ensuring a successful repair outcome.
Personal Protective Equipment (PPE) Requirements
When undertaking repairs on an air conditioning (AC) compressor, particularly in areas like Tulsa where the climate can be quite warm, wearing adequate personal protective equipment (PPE) is a critical component of the job. PPE serves as the first line of defense against potential hazards one might encounter during repair work. The essential items of PPE include safety goggles, gloves, and appropriate clothing, such as long sleeves and durable work pants. These items protect the technician from physical injuries, debris, and chemicals that could cause harm during the repair process.
Safety goggles are vital, especially when handling tools or components that might release debris during disassembly. In the case of AC compressors, technicians may encounter sharp edges or potentially hazardous substances, making eye protection indispensable. Gloves, preferably of a heavy-duty material resistant to cuts and chemicals, are necessary to protect the hands from the sharp components and refrigerants that may leak during the repair process. Furthermore, closed-toe shoes with grips are essential to prevent slips and provide protection against falling equipment.
Proper attire also plays a role; loose clothing can catch in machinery, causing injuries, while synthetic fibers can melt due to heat sources, resulting in severe burns. Thus, wearing tightly fitted, flame-resistant clothing is advisable. Additionally, in areas with high humidity or heat, maintaining hydration and taking regular breaks is crucial for physical well-being. The use of personal protective equipment not only ensures the safety of the technician but also aligns with proper workplace safety protocols, minimizing the risk of injury or illness during AC compressor repairs.
In Tulsa, where the heat can become oppressive, it’s essential to incorporate safety precautions beyond simply wearing PPE. Before beginning the repair, technicians should assess their environment and ensure that they are working in a well-ventilated area to avoid inhaling any harmful fumes or substances. This is particularly important when dealing with refrigerants, as they can pose respiratory risks. It’s also advisable to have first aid equipment readily available in case of emergencies. Overall, a commitment to proper PPE is foundational to the safety of HVAC technicians and contributes to effective work practices within the field.
Electrical Safety Measures
When it comes to repairing an AC compressor in Tulsa, implementing strict electrical safety measures is crucial to ensure the safety of both the technician and the equipment. Electrical components are integral to the functioning of an AC unit, and any work on these components presents inherent risks, including electrical shocks, equipment damage, and even potential fire hazards. Therefore, it is essential to adhere to best practices that minimize these risks.
Firstly, one of the primary precautions is to always disconnect power before starting any repair work. This usually involves turning off the circuit breaker or disconnect switch that supplies electricity to the AC unit. It’s advisable to double-check that power is indeed disconnected using a multimeter or a voltage tester. This step cannot be overstated, as it is vital for preventing electrical shocks. Moreover, technicians should be familiar with the wiring and electrical schematics of the AC system they are working on, allowing them to understand the flow of electricity and identify any parts that may present a risk.
Additionally, using insulated tools is recommended to further guard against electrical hazards. Insulated tools are designed to protect against electrical current, providing an extra layer of security for the technician. Technicians should also consider wearing rubber-soled shoes to provide additional insulation from electrical shocks while working on the unit. Furthermore, maintaining a dry work environment is essential. Water, or even humidity, can significantly increase the risk of electrical accidents, so keeping the area clear of any moisture is prudent.
Another important aspect of electrical safety is ensuring that all components are in good condition before re-energizing the system. This includes checking for damaged wires, loose connections, or any burn marks that might indicate overheating. All electrical components should be thoroughly inspected for signs of wear or malfunction before putting the system back into operation. After completing the repairs, technicians should follow proper startup procedures and monitor the system carefully for any irregularities.
In conclusion, taking the necessary electrical safety measures during AC compressor repairs in Tulsa is not just a best practice; it is a fundamental requirement that protects the technician and ensures the reliable operation of the equipment. By understanding the risks involved, utilizing insulated tools, maintaining a safe work environment, and reviewing all connections and components, technicians can perform their repairs efficiently and safely.
Handling Refrigerants Safely
When it comes to repairing an air conditioning (AC) compressor, handling refrigerants safely is one of the most critical aspects of the process. Refrigerants, such as R-410A or R-22, are substances used in AC systems to absorb and release heat, enabling cooling. However, these chemicals can pose significant health risks and environmental hazards if not managed properly. They can cause skin irritation, respiratory issues, or even be harmful to the ozone layer if released into the atmosphere. Therefore, understanding how to handle refrigerants safely is essential for any technician working in Tulsa or anywhere else.
Firstly, technicians must be familiar with the specific type of refrigerant used in the AC system they are servicing. Each refrigerant has its properties and safety considerations. For example, some refrigerants can be flammable, while others can cause asphyxiation or toxic exposure if inhaled. Technicians should always refer to the Material Safety Data Sheets (MSDS) for the refrigerants they are working with to understand the potential hazards and recommended safety measures.
Proper personal protective equipment (PPE) is a must when handling refrigerants. This includes wearing gloves, safety goggles, and appropriate clothing to minimize skin contact and avoid inhalation of any vapor or gas. Ensuring good ventilation in the working area is also crucial since some refrigerants can displace oxygen, leading to a risk of suffocation. Furthermore, technicians should employ leak detection methods to identify any potential refrigerant leaks during the repair process. Using tools designed for refrigerant handling, such as recovery machines and vacuum pumps, ensures that refrigerants are captured and disposed of correctly, thus protecting both the technician and the environment.
In Tulsa, adherence to local regulations is crucial when handling, recycling, or disposing of refrigerants. The Environmental Protection Agency (EPA) has strict guidelines about refrigerant management, which technicians must follow. This includes proper recovery methods before opening the system to prevent the release of refrigerants into the atmosphere. By following these safety protocols and understanding the importance of proper handling, technicians not only safeguard their health and safety but also contribute to environmental protection and compliance with legal requirements.
Lockout/Tagout Procedures
Lockout/Tagout (LOTO) procedures are critical safety protocols implemented in various industries, including HVAC repair, to prevent unexpected machine start-up or the release of stored energy during maintenance activities. When repairing an AC compressor, proper LOTO procedures help safeguard technicians from potentially dangerous situations. These procedures involve using locks and tags to ensure that equipment cannot be operated while maintenance work is being conducted.
To effectively carry out LOTO procedures, technicians must first identify all energy sources—including electrical, mechanical, hydraulic, pneumatic, and thermal sources—associated with the AC compressor. Once identified, these sources should be isolated using appropriate means such as circuit breakers or shut-off switches, and then locked out with a physical lock. Tags should be placed on the equipment to warn others that maintenance is taking place, indicating that the equipment should not be operated under any circumstances.
Training is paramount in ensuring that all personnel understand and correctly follow LOTO procedures. This includes knowing how to apply and remove locks and tags, recognizing the types of energy present, and understanding the specific protocols for the equipment being serviced. Regular audits and safety meetings can reinforce the importance of these procedures and ensure compliance. By adhering to LOTO procedures, technicians in Tulsa can significantly reduce the risk of accidents and enhance their safety while performing AC compressor repairs.
In addition to LOTO, it is essential to maintain clear communication among team members. Before beginning work, technicians should conduct a safety briefing to discuss the tasks, procedures, and any specific hazards involved. Furthermore, all workers involved in the repair process should be aware of the LOTO status of the equipment to prevent any accidental re-energization. Ensuring these safety precautions are followed will help protect everyone in the vicinity of the repair work and promote a culture of safety within the workplace.
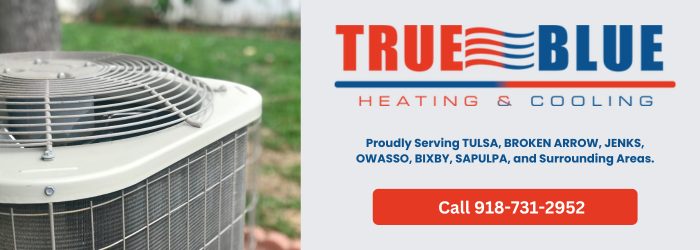
Environmental Considerations and Hazardous Waste Disposal
When it comes to repairing an AC compressor, particularly in a place like Tulsa, understanding environmental considerations and managing hazardous waste disposal is paramount. AC systems often contain various materials that can pose environmental risks if not handled properly. This includes refrigerants, oils, and other fluids that may have harmful properties. Technicians must be aware of the regulations that govern the disposal of these materials to prevent environmental contamination and ensure compliance with local and federal laws.
One critical aspect of environmental considerations is the potential release of refrigerants into the atmosphere. Some refrigerants are known to be greenhouse gases that can contribute to global warming. Therefore, when servicing or repairing an AC compressor, it is essential to take steps to capture and reclaim refrigerants. This typically involves using appropriate recovery equipment to remove the refrigerant from the system before any repair work begins. It is also vital to ensure that all refrigerants are reused, recycled, or disposed of in compliance with Environmental Protection Agency (EPA) regulations.
Proper disposal of hazardous waste, such as oil and worn-out parts, also requires special attention. Technicians should follow all guidelines for the disposal of items that may contain dangerous substances. This includes using designated recycling and waste disposal facilities that can handle hazardous materials. In Tulsa, local regulations may specify particular procedures or facilities where such waste can be disposed of safely. By adhering to these regulations, technicians not only protect the environment but also reduce the risk of legal liability related to improper waste disposal practices.
In summary, when repairing an AC compressor, it’s crucial to consider environmental impact and implement proper hazardous waste disposal methods. This reflects a commitment to both environmental stewardship and compliance with regulations. Taking these precautions not only safeguards the ecosystem but also fosters a sense of responsibility among technicians, emphasizing the importance of sustainability in everyday practices.