When it comes to maintaining a comfortable and efficient indoor environment, a well-functioning HVAC (Heating, Ventilation, and Air Conditioning) system is essential. In Tulsa, where the climate can range from sweltering summers to chilly winters, regular inspections of HVAC systems are crucial for ensuring comfort, improving energy efficiency, and extending the life of the equipment. An HVAC system inspection involves a thorough assessment of all components, from the heating and cooling units to the ductwork and ventilation systems, enabling homeowners and business operators to identify potential issues before they escalate into costly repairs.
During an HVAC system inspection in Tulsa, certified technicians undertake a comprehensive evaluation of the system’s functionality and efficiency. This includes checking the thermostat settings, examining the filters, testing for proper airflow, and inspecting the refrigerant levels in air conditioning units. Additionally, technicians will look for signs of wear and tear, corrosion, or any operational inefficiencies that could hinder performance. With the fluctuating weather patterns in the region, understanding the nuances of local HVAC needs and regulations further enhances the importance of these inspections.
Beyond merely detecting problems, an HVAC inspection helps in enhancing energy efficiency, which is increasingly paramount in today’s eco-conscious society. Energy costs can soar during extreme weather, and an inefficient system can significantly impact a home’s carbon footprint. Therefore, understanding what an HVAC system inspection entails can empower property owners in Tulsa to take proactive steps toward maintaining their systems, ensuring their comfort while promoting sustainability. In this article, we will delve into the key components of an HVAC inspection, the benefits of regular maintenance, and the specific considerations for residents of Tulsa looking to optimize their indoor climate.
Visual Inspection of Equipment and Components
A visual inspection of equipment and components is a crucial first step in an HVAC system inspection. This process involves a thorough examination of the visible parts of the heating, ventilation, and air conditioning system to identify any obvious issues or signs of wear and tear. Inspectors typically check the major components, such as the furnace, air conditioner, heat pump, and ductwork, looking for any signs of physical damage, corrosion, or deterioration. During this inspection, the technician assesses the condition of the system’s individual parts, including belts, motors, fans, and filters.
In addition to assessing the condition of the equipment itself, the inspector also examines the installation and positioning of these components. For instance, if an air conditioning unit is installed in a location that does not allow for adequate airflow or is too close to obstructions, it can lead to efficiency problems and potential breakdowns. Furthermore, the inspector looks for any modifications to the equipment that may not be code compliant or safe, ensuring that the system is in adherence to local regulations and manufacturer recommendations.
In Tulsa, a city with varying temperatures across seasons, it is especially important to ensure that HVAC systems are well-maintained. A visual inspection can reveal issues early on, before they develop into costly repairs or system failures. Common visual indicators that may prompt further investigation include unusual noises from the system, abnormal exhaust emissions, or uneven heating and cooling throughout the home. By taking the time to conduct a detailed visual inspection, homeowners can significantly improve the reliability and longevity of their HVAC systems, ensuring comfort throughout the year and energy efficiency, which can lead to lower utility bills. Overall, this preliminary assessment sets the stage for the more comprehensive tests and checks that follow in a complete HVAC system inspection.
Testing of Heating and Cooling Performance
Testing of heating and cooling performance is a critical component of an HVAC system inspection, particularly in climates that experience wide temperature variations like Tulsa’s. This process involves assessing the capacity and efficiency of both the heating and cooling systems to ensure they meet the required comfort levels in residential or commercial spaces. The technician evaluates how effectively the heating system can warm the indoor environment during colder months and how well the cooling system can lower the temperature during the hotter months.
During this performance testing, several specific actions are undertaken. First, the technician will check the thermostat calibration to ensure that it accurately reflects the desired temperature settings. Next, the technician typically measures the temperature differential between the air entering and exiting the HVAC system. This measurement helps determine if the system is functioning within its designed parameters. A significant imbalance may indicate issues that could lead to increased energy consumption and might even point to underlying mechanical problems, such as duct leaks or refrigerant issues.
Another aspect of testing heating and cooling performance involves inspecting the air filters and overall airflow. Restricted airflow can significantly hinder system efficiency and performance, leading to increased wear and tear on components. The technician will also check the refrigerant levels in cooling systems to ensure that there is no leakage and that the system operates within the manufacturer’s specifications. Low refrigerant levels can affect the system’s ability to cool effectively and might require additional servicing or repairs.
In summary, testing of heating and cooling performance is an essential part of an HVAC inspection in Tulsa, involving a comprehensive evaluation of system operations, airflow, and temperature regulation. This thorough assessment helps to identify any operational inefficiencies or potential failures and allows homeowners to make informed decisions about maintenance or necessary repairs to ensure their systems are running optimally throughout the year.
Examination of Ductwork for Leaks and Insulation
The examination of ductwork is a critical component of an HVAC system inspection, particularly in Tulsa, where climatic conditions can vary significantly throughout the year. Proper ductwork assessment ensures that the system operates efficiently, providing adequate heating and cooling while minimizing energy consumption and costs. During an inspection, HVAC professionals thoroughly examine the ductwork for any leaks, which are common culprits of energy loss and can lead to fluctuations in indoor temperature and air quality.
Identifying leaks in the ductwork is crucial, as even small openings can dramatically reduce the system’s efficiency. Technicians typically employ various methods, such as visual inspections, smoke testing, or specialized tools like thermal cameras to detect temperature differences that indicate air leaks. Once leaks are identified, they can be sealed using appropriate materials such as mastic sealants or foil tape, thus improving system efficiency and reducing energy waste.
In addition to checking for leaks, the insulation of the ductwork is also evaluated. Proper insulation prevents heat loss in the winter and keeps the conditioned air cool in the summer, which is particularly important in a region like Tulsa, where seasonal temperature variations can be significant. Insufficient insulation can lead to excessive energy use and discomfort due to temperature imbalances in different areas of the home or building.
Overall, a thorough examination of the ductwork during an HVAC inspection is essential for ensuring the system’s overall performance and reliability. Addressing any identified issues not only extends the life of the HVAC system but also enhances indoor air quality, as well-sealed and insulated ducts minimize the entry of dust, allergens, and other pollutants. Consequently, regular ductwork examinations are a wise investment for maintaining a comfortable and energy-efficient environment.
Electrical and Safety Checks
When it comes to maintaining the efficiency and safety of HVAC systems, electrical and safety checks are critical components of a thorough inspection. These checks are designed not only to ensure that the system is functioning adequately but also to protect occupants from potential hazards associated with electrical issues, such as short circuits, electric shocks, and even fire risks.
During the electrical check, technicians will start by examining the wiring and connections for signs of wear, damage, or corrosion. This includes looking at the electrical panel, disconnect switches, and fuses to ensure they are properly rated and functioning correctly. They will test the electrical components, including the thermostat, relays, and contactors, to ensure they are operating as they should. It’s crucial that all electrical connections are secure and free of any signs of overloading or deterioration, as these can lead to overheating and other serious safety concerns.
Safety checks are equally important and can involve examining the HVAC system for compliance with local codes and regulations. Technicians will verify that the system has adequate safety controls operational, such as pressure relief valves and temperature sensors. They will also check emergency shut-off switches to ensure they function correctly, in case an immediate response is needed to prevent an accident. This aspect of the inspection reassures homeowners that their HVAC system is safe to operate and reduces the risk of dangerous incidents.
In summary, the electrical and safety checks within an HVAC system inspection are essential for ensuring not only the efficiency of the system but also the safety of the home and its occupants. Regular inspections that include these checks can help identify potential issues before they become serious problems, leading to safer operation and potentially lower energy costs as the system runs more efficiently. Whether in Tulsa or elsewhere, these assessments form a foundational part of HVAC maintenance, emphasizing the importance of professional oversight and regular servicing.
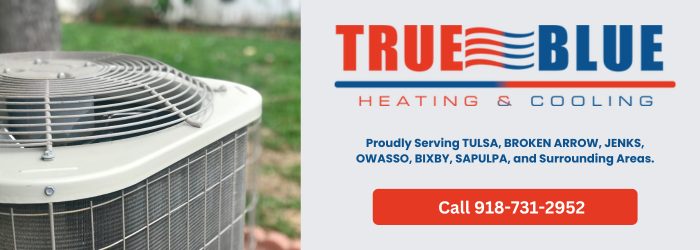
Filter Assessment and Maintenance Recommendations
One of the critical components of an HVAC system inspection in Tulsa is the filter assessment and subsequent maintenance recommendations. Filters play a pivotal role in ensuring that air quality is maintained within the home, as they capture dust, dirt, allergens, and other debris that can hinder the effectiveness of the heating and cooling system. An HVAC system with dirty or clogged filters can lead to various issues, including reduced airflow, increased energy usage, and potential damage to the system itself.
During an inspection, technicians evaluate the condition of the air filters, noting any signs of excessive dirt accumulation or damage. A clean filter promotes optimal airflow, reduces strain on the HVAC unit, and improves indoor air quality by filtering out pollutants. Technicians will typically check how often the filters have been replaced or cleaned, as this can vary based on factors such as pet presence, smoking indoors, or proximity to construction areas that may generate dust.
Following the assessment, HVAC professionals will provide recommendations on when to change or clean air filters based on their findings. They may advise homeowners on the type of filter that would be best suited for their needs, considering factors like efficiency ratings (MERV ratings) and compatibility with existing systems. Moreover, technicians may emphasize a proactive maintenance schedule, encouraging homeowners to routinely check and replace filters every one to three months, depending on usage and environmental conditions. By adhering to these recommendations, homeowners in Tulsa can ensure their HVAC system operates efficiently, extends its lifespan, and maintains a healthy indoor air environment.