When it comes to maintaining comfortable indoor environments, Heating, Ventilation, and Air Conditioning (HVAC) systems play a pivotal role. For residents and businesses in Tulsa, Oklahoma, ensuring that these systems are not only effective but also compliant with local regulations is crucial. Compliance with HVAC standards is essential for health, safety, and environmental considerations, as well as for the legal and financial integrity of properties. However, navigating the complexities of HVAC compliance can often present unique challenges, particularly in a city like Tulsa where the climate’s extremes can exacerbate the risks associated with non-compliance.
In Tulsa, typical HVAC compliance issues can arise from several sources, including outdated equipment, lack of proper installation, and insufficient maintenance practices. Equipment must be up to code, meeting both federal and local environmental regulations, particularly with respect to energy efficiency and refrigerant usage. The significance of following the guidelines established by certification bodies such as the Environmental Protection Agency (EPA) and local ordinances cannot be overstated, as violations not only pose risks to occupants but can also lead to substantial penalties for property owners and operators.
Additionally, ongoing maintenance and regular inspections are critical in averting compliance issues. Inconsistent service schedules can lead to deteriorating efficiency and increased emissions, thereby violating local air quality standards. This is particularly relevant for Tulsa, where air quality is a significant concern. Moreover, lack of awareness regarding updated compliance regulations can leave both installers and users vulnerable to costly repercussions. Understanding the most common compliance issues in HVAC systems can empower Tulsa residents to better prepare and safeguard their environments, ensuring that their systems not only provide comfort but also align with regulatory expectations. As we delve deeper into this essential topic, we will explore these typical compliance issues and offer insights on how to effectively address and overcome them.
Local Code Compliance and Regulations
Local code compliance and regulations are crucial aspects of HVAC (Heating, Ventilation, and Air Conditioning) systems in any given area and particularly in Tulsa, Oklahoma. Compliance with local codes ensures the safety, efficiency, and reliability of HVAC systems. These codes are designed to protect both the occupants of a building and the environment by establishing minimum standards for system design, installation, operation, and maintenance. In Tulsa, the city enforces various building codes and regulations that HVAC contractors must adhere to when designing and installing systems in residential, commercial, and industrial buildings.
One of the primary compliance issues in Tulsa relates to the ever-evolving nature of building codes. Local regulations may change, and contractors need to stay informed about those changes to ensure that their installations meet current safety and efficiency standards. This is particularly important for energy efficiency codes, as local governments often aim to reduce energy consumption and environmental impact. Non-compliance can lead to various issues ranging from fines and penalties imposed by municipal authorities to more severe consequences, such as needing to redo installations that do not meet the code or require costly repairs.
Moreover, there are often specific codes pertaining to zoning and space utilization as they relate to HVAC systems. For instance, some residential areas may have restrictions on where outdoor condensing units can be placed. Similarly, commercial buildings may need to ensure compliance with occupancy requirements, which can directly affect sizing and airflow specifications. Understanding these parameters is essential for HVAC contractors to mitigate non-compliance issues.
Furthermore, proper documentation is critical in demonstrating compliance. Contractors must keep accurate records of their work, including permits, inspections, and any modifications made to existing systems. When these records are lacking or improperly managed, it can create additional regulatory challenges and can even affect future property transactions.
In summary, local code compliance and regulations are foundational to the installation and operation of HVAC systems in Tulsa. Adhering to these regulations ensures safety, efficiency, and functionality, protecting both residents and contractors from potential legal and financial consequences. It emphasizes the need for HVAC professionals to remain informed and diligent in their practices to navigate the complexities associated with compliance successfully.
Permitting and Inspection Challenges
Permitting and inspection challenges are significant hurdles in the HVAC industry, particularly in cities like Tulsa. When a new HVAC system is installed or an existing system is modified, securing the appropriate permits from local authorities is essential. This process ensures that all installations comply with local codes, safety standards, and environmental regulations. Inadequate or improper permitting can result in fines, project delays, and additional costs for property owners and contractors alike.
One of the main issues that arise during the permitting phase is the complexity and variability of regulations across different jurisdictions. Contractors often find it challenging to navigate the local government’s requirements, which can lead to mistakes in submitting necessary documents and drawings. Moreover, varying interpretations of the codes by different inspectors can further complicate compliance, resulting in the need for multiple inspections or reworks, prolonging project timelines.
Inspection challenges also pose significant issues, as HVAC systems must meet strict operational and safety standards after installation. Inspectors check for proper installation procedures, system efficiency, and compliance with zoning laws, which can lead to complications if systems do not pass initial inspections. Home and business owners may face setbacks if their systems do not meet code requirements or if the correct inspections are not conducted in a timely manner. Occasionally, faulty or delayed inspections can hinder a project’s progress, resulting in suspended operations until compliance is achieved.
Additionally, the impact of seasonal demands can exacerbate permitting and inspection challenges. During peak seasons, such as summer and winter, the volume of HVAC installations typically increases, leading to an influx of permit applications. This can create a backlog in processing and scheduling inspections, leaving contractors and customers frustrated with extended timelines. To mitigate these challenges, effective communication between service providers, building owners, and local municipalities is crucial to facilitate smoother permitting and inspection processes, ensuring that compliance issues are addressed proactively rather than reactively.
HVAC Equipment Standards and Efficiency Requirements
HVAC equipment standards and efficiency requirements are crucial components of building codes and energy regulations in Tulsa, as they ensure that heating, ventilation, and air conditioning systems operate effectively while minimizing energy consumption and environmental impact. These standards are set by various organizations, including the U.S. Department of Energy (DOE) and the Environmental Protection Agency (EPA), along with local jurisdictional regulations that may impose additional requirements specifically tailored to Tulsa’s climate and energy goals.
One of the main focuses of these standards is energy efficiency. Energy-efficient HVAC equipment is designed to consume less energy while providing the same or improved levels of comfort. In Tulsa, the Seasonal Energy Efficiency Ratio (SEER) and the Annual Fuel Utilization Efficiency (AFUE) ratings are commonly referenced metrics that indicate how well HVAC systems convert energy into useful heating or cooling. Installers and contractors must be well-versed in these standards to ensure compliance, not only for legal reasons but also to promote sustainable practices.
In addition to efficiency regulations, there are specific equipment requirements that must be adhered to, including the use of certain refrigerants and the design specifications of HVAC units. For instance, older units that utilize refrigerants with high global warming potential may be phased out in favor of newer, more environmentally friendly alternatives. Compliance with these standards is essential to avoid penalties and to ensure the safety and health of occupants, as improperly installed or outdated equipment can lead to serious issues such as carbon monoxide leaks or poor indoor air quality.
Typical HVAC compliance issues in Tulsa often revolve around misunderstandings of these complex standards. Contractors may inadvertently use equipment that does not meet local efficiency requirements, or they may neglect to properly document compliance during inspections. This can result in costly fines and the need for retrofitting systems long after installation. Furthermore, as energy codes evolve to promote greener technologies, staying up-to-date with such changes is essential for HVAC professionals to ensure successful compliance and continued service licensure in the industry. Engaging with training and certification programs can greatly enhance a contractor’s ability to navigate these regulations effectively.
In summary, adhering to HVAC equipment standards and efficiency requirements is not just a matter of legal compliance; it is also integral to promoting energy conservation and ensuring the well-being of Tulsa’s residents. Understanding and implementing these standards helps mitigate common compliance issues, ultimately leading to a more sustainable future for the community.
Indoor Air Quality and Ventilation Regulations
Indoor air quality (IAQ) is a critical component of HVAC regulations, particularly in urban areas like Tulsa. Adequate ventilation is essential to ensure that indoor environments are healthy and conducive to the well-being of the occupants. The regulations governing IAQ and ventilation typically address the minimum acceptable standards for air circulation, filtration, and pollutant levels within a building. These guidelines are put in place to prevent the accumulation of harmful substances and to maintain comfort levels through effective temperature and humidity control.
In Tulsa, typical HVAC compliance issues related to IAQ often arise from outdated systems that are incapable of filtering airborne contaminants effectively or providing sufficient fresh air. Properties without proper ventilation systems may fail to meet the prescribed airflow rates, resulting in stuffy, uninhabitable spaces prone to moisture buildup, mold proliferation, and health problems for the occupants. Furthermore, buildings built before modern ventilation standards were implemented may lack adequate duct systems, making it difficult to both bring in fresh air and expel stale air.
Another common issue within the scope of indoor air quality is the lack of awareness or adherence to proper maintenance practices. Over time, HVAC systems can accumulate dust, allergens, and pollutants, which can be recirculated throughout the indoor environment if not properly maintained. This emphasizes the importance of regular inspections and service to ensure that air filters are replaced and that ductwork is cleaned, in order to uphold both air quality standards and regulatory compliance.
Ultimately, addressing indoor air quality and ventilation regulations is essential not only for legal compliance but also for the health and comfort of building occupants in Tulsa. Ensuring that systems are up to date and competent in managing air quality will significantly reduce the likelihood of legal complications and improve the overall environment within residential and commercial buildings alike. Local HVAC professionals must stay informed about these regulations, as they play a crucial role in both design and maintenance of systems that meet the required standards.
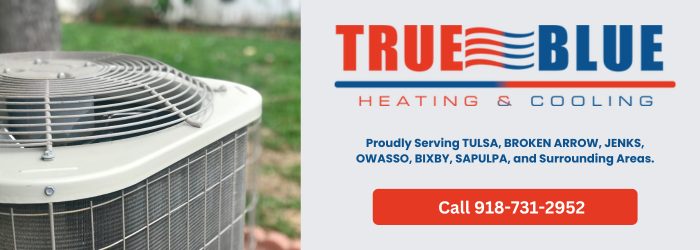
Common Installation and Maintenance Violations
In the realm of HVAC systems, common installation and maintenance violations can lead to significant issues not only for compliance with local regulations in Tulsa but also for the efficiency and safety of the systems themselves. These violations are often attributed to improper installation practices, lack of regular maintenance, or deviations from manufacturer specifications. For instance, one prevalent installation violation includes oversizing or undersizing the HVAC unit. This can lead to inefficient operation, increased energy consumption, and ultimately higher utility bills. An incorrectly sized unit may cycle on and off more frequently, leading to undue wear and tear and decreased lifespan.
Another frequent violation occurs when ductwork is poorly installed or lacks proper sealing. Leaky ducts can significantly lower system efficiency as conditioned air escapes before reaching the intended areas. This not only causes discomfort but also leads to higher energy costs. Additionally, using unapproved materials for duct insulation or failing to insulate ducts located in unconditioned spaces can compromise system performance and violate local code requirements.
Maintenance violations are equally critical. Neglecting regular maintenance tasks, such as changing filters or failing to clean coils, can result in reduced system efficiency and contribute to indoor air quality issues. In Tulsa, there may also be specific requirements for maintenance checks and documentation, and failing to adhere to these guidelines can result in compliance violations. Regular maintenance is not just about ensuring comfort; it is essential for safety, particularly concerning the risk of carbon monoxide leaks or other hazardous conditions that may arise from poorly maintained gas-fired systems.
In summary, ensuring compliance in HVAC installations and maintenance within Tulsa requires attention to detail and adherence to local codes and regulations. Bypassing these standards not only risks legal repercussions but can also have detrimental impacts on system performance, energy efficiency, and occupant safety. Homeowners and HVAC professionals alike must prioritize proper installation techniques and consistent maintenance practices to avoid common violations and uphold the integrity of HVAC systems.