As temperatures soar in Tulsa during the sweltering summer months, commercial air conditioning (AC) units become essential for maintaining comfortable indoor environments in business spaces and public facilities. However, like any complex system, these units can experience a range of problems that not only affect their performance but can also lead to decreased energy efficiency, increased operational costs, and even potential safety hazards. For business owners and facility managers in Tulsa, understanding the common issues associated with commercial AC units is crucial for ensuring optimal performance and prolonging the lifespan of these vital systems.
In this article, we will delve into the most prevalent problems faced by commercial AC units in Tulsa. From inconsistent cooling and refrigerant leaks to malfunctioning thermostats and airflow problems, each of these issues can significantly disrupt operations and impact comfort levels for employees and customers alike. Moreover, Tulsa’s unique climate, characterized by hot summers and unpredictable weather patterns, can exacerbate these challenges, making it even more essential for businesses to be vigilant in identifying and addressing potential AC failures.
In addition to identifying these common AC problems, we will also explore the underlying causes and preventive measures that can be taken to mitigate issues before they escalate. Understanding the mechanics of commercial AC systems and recognizing the early warning signs can help business owners take proactive steps, ensuring their units operate efficiently when they are needed most. Whether you’re a seasoned facility manager or a new business owner, this exploration into common commercial AC problems in Tulsa will provide valuable insights to enhance your understanding and streamline the maintenance of your heating, ventilation, and air conditioning systems.
Refrigerant Leaks
Refrigerant leaks are a significant issue for commercial air conditioning (AC) units, especially in places like Tulsa where the climate can demand heavy use of cooling systems. Refrigerant is the lifeblood of an air conditioning system; it circulates within the unit to absorb heat and provide cool air into the building. When leaks occur, the efficiency of the AC unit can drastically decrease, leading to higher energy consumption and increased costs for operation. Additionally, low refrigerant levels can cause the system to work harder to maintain desired temperatures, which can lead to premature wear and a higher likelihood of component failure.
The causes of refrigerant leaks can vary, but they often stem from factors such as wear and tear over time, corroded or damaged piping, and improper installation. In commercial settings, where units are under constant use, these issues can become pronounced. Moreover, environmental factors like temperature fluctuations and even sediment accumulation can contribute to leak development. Businesses in Tulsa must be vigilant about monitoring their systems, as a small refrigerant leak can not only affect cooling performance but also pose environmental risks and lead to costly repairs down the line.
Addressing refrigerant leaks typically requires professional attention, as it involves identifying the source of the leak, repairing it, and then recharging the system with the proper amount of refrigerant. Regular maintenance checks can help detect these leaks early, mitigating the potential damage to the AC unit. Neglecting this aspect can lead to further complications, such as damage to the compressor or other essential components, ultimately resulting in a complete system failure which may require a full replacement. To maintain optimal efficiency, it’s crucial for Tulsa’s businesses to prioritize addressing refrigerant leaks promptly and effectively.
Electrical Issues
Electrical issues in commercial air conditioning (AC) units can manifest in various forms and may lead to performance inefficiencies or complete system failures. These problems often stem from several factors, including faulty wiring, poor connections, circuit breaker failures, or issues with the thermostat. In a commercial setting, where large spaces and numerous systems rely on heating, ventilation, and air conditioning (HVAC) equipment for comfort, these electrical problems can disrupt operations and lead to uncomfortable working conditions.
One prevalent electrical issue is the overheating of components or wiring. This can occur when the AC unit is overworked, perhaps due to poor airflow caused by clogged filters or blocked ducts. When the system has to work harder, it places excessive strain on the electrical components, which can lead to burnout or even fire hazards. It’s essential to regularly check and maintain the electrical components to safeguard against such overloading situations, ensuring that circuits are not compromised and that the correct voltage is supplied consistently.
Another common electrical issue involves the failure of the thermostat, which acts as the control center for the AC unit. A malfunctioning thermostat can lead to improper temperature readings, causing the unit to either work harder than necessary or not activate when needed. This can not only result in discomfort but also increased operational costs due to higher energy consumption. Regular testing and calibration of the thermostat are necessary to ensure the system operates at its optimal level.
In Tulsa, businesses often encounter particular environmental conditions that exacerbate these electrical issues. For instance, high humidity levels and extreme temperatures can put additional strain on AC systems. Furthermore, poorly designed electrical systems in older buildings may not be equipped to handle the demands of modern HVAC units, leading to frequent blowouts of breakers or electrical failures. Regular inspections and timely repairs are crucial to addressing these problems before they escalate, ensuring a reliable and efficient cooling system in commercial establishments.
Clogged Drain Lines
Clogged drain lines are a common issue that can plague commercial air conditioning (AC) units, especially in humid climates like Tulsa. These drain lines are responsible for removing the condensation that forms on the evaporator coils of the AC unit. When the system is functioning correctly, moisture is collected and channeled away from the unit and out of the building. However, over time, debris such as dirt, dust, mold, and algae can accumulate within these drain lines, leading to blockages.
When drain lines become clogged, it typically leads to a backup of water within the unit. This can cause significant operational issues, including water damage to the surrounding areas and potential damage to the AC system itself. In commercial settings, where downtime can lead to loss of productivity or revenue, such disruptions can be particularly costly. If the backup continues, it might eventually trigger the unit’s safety features, shutting down the AC system to prevent further damage.
Moreover, clogged drain lines can contribute to indoor air quality problems. The stagnant water can become a breeding ground for mold and bacteria, which can then enter the air circulated throughout the building. This not only poses health risks to occupants but could also lead to more extensive issues that require professional remediation. Regular maintenance and cleaning of drain lines are critical steps in ensuring the efficiency and longevity of commercial AC units, helping to prevent these kinds of problems from arising in the first place.
In Tulsa, where the weather can be quite humid, property owners and facility managers need to be particularly vigilant about routine inspections and maintenance. Regularly checking and clearing drain lines can help mitigate the risk of clogs and their subsequent consequences, thus keeping commercial AC systems running smoothly and ensuring a comfortable environment for employees and clients alike.
Inefficient Cooling Performance
Inefficient cooling performance is a common issue faced by commercial air conditioning (AC) units, particularly in climates that experience significant heat, such as Tulsa. This problem manifests when the AC system fails to adequately cool the indoor environment, leading to uncomfortable temperatures and increased operational costs. Several factors can contribute to this deficiency, including inadequate system sizing, aging equipment, or poor maintenance practices. For instance, if an AC unit is undersized for the space it is intended to cool, it may struggle to maintain set temperatures, causing it to work harder and consume more energy than necessary.
Another contributing factor to inefficient cooling performance can be the dirty or blocked components within the system. Over time, dust and debris can accumulate on the evaporator coils, condenser coils, and air filters, restricting airflow and reducing the heat exchange process. This not only hinders the cooling ability of the unit but also increases wear and tear on the system, potentially leading to more significant breakdowns in the future. Property owners must ensure that the AC units are regularly maintained and that filters are replaced or cleaned as needed to maximize efficiency.
Furthermore, refrigerant issues can also lead to inefficient cooling. If an AC unit has a refrigerant leak, it can’t absorb as much heat from the indoor air, resulting in insufficient cooling. An improper refrigerant charge can create similar problems, affecting the system’s overall performance and leading to higher energy bills. Therefore, it is crucial for business owners in Tulsa to be aware of these potential problems and implement proactive maintenance strategies to ensure optimal cooling function. Regular inspections by qualified technicians can help detect inefficiencies early, minimizing downtime and maintaining a comfortable environment for both employees and customers.
In summary, addressing issues related to inefficient cooling performance not only improves comfort but also enhances energy efficiency and prolongs the lifespan of commercial AC units, ultimately benefiting the bottom line of businesses in Tulsa.
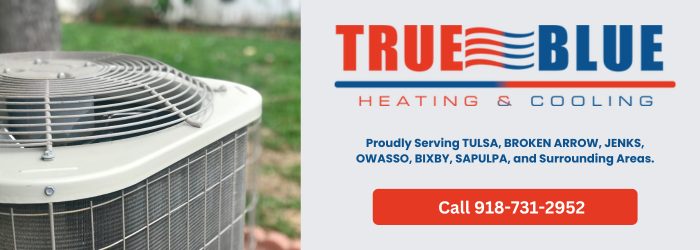
Regular Maintenance and Inspection Challenges
Regular maintenance and inspection challenges are significant issues faced by commercial air conditioning units, especially in regions like Tulsa, where the climate can demand heavily on HVAC systems. Many business owners often overlook the importance of regular maintenance, assuming that if the system is working, there is no immediate need for inspections or upkeep. This oversight can lead to larger problems down the road, including diminished efficiency and increased repair costs.
One of the primary challenges in maintaining commercial AC units is the complexity and scale of these systems. Unlike residential units, commercial HVAC systems are typically larger and serve multiple zones, making inspections and maintenance more involved. Additionally, the frequency of use and the demands placed on these systems, particularly during the sweltering summers in Tulsa, can exacerbate wear and tear. This means that without a comprehensive maintenance schedule, components can become neglected, leading to breakdowns that could have been prevented.
Another issue is the lack of trained personnel to conduct thorough inspections. Many businesses either do not have in-house maintenance teams or rely on external contractors who may not be familiar with the specific needs of the system they are working on. This gap can result in inadequate maintenance checks, which can miss critical indicators of potential failures. Furthermore, the cost associated with regular maintenance can deter businesses from pursuing it, leading to a false economy—spending less now might result in costly repairs or replacements later on.
Ultimately, regular maintenance and inspection challenges can significantly affect the longevity and performance of commercial AC units in Tulsa. Addressing these challenges with a proactive approach tailored to the specific operating conditions can help ensure that these systems run efficiently, thereby reducing the likelihood of breakdowns and costly repairs in the future.