When the sweltering heat of an Oklahoma summer descends upon Tulsa, a dependable air conditioning system becomes a cornerstone of comfort in both residential and commercial spaces. Regular air conditioning inspections are essential for maintaining the efficiency and reliability of these systems, ensuring that they can withstand the demands of high temperatures. However, during these inspections, technicians often identify a variety of common problems that, if left unaddressed, can lead to diminished performance, increased energy costs, and even premature system failure.
Understanding the potential issues that can arise during AC inspections is crucial for homeowners and business owners alike. From minor glitches that can be easily repaired to more significant concerns that may require extensive repairs or even replacement, recognizing the signs of trouble can help individuals take proactive measures to protect their investment. Among the most frequently observed issues are inadequate airflow, refrigerant leaks, electrical failures, and clogged filters, which can hinder the system’s overall functionality and efficiency.
In addition to the mechanical and technical challenges, neglecting regular AC inspections can have ripple effects on energy consumption and indoor air quality. As systems struggle to operate optimally, they may consume more electricity, leading to sky-high utility bills. Moreover, problems such as mold growth, duct leaks, and unclean filters can compromise the quality of the air circulating within a home or office, posing health risks to occupants. By shedding light on the common problems encountered during AC inspections in Tulsa, this article aims to equip readers with the knowledge they need to recognize the importance of routine maintenance and the steps they can take to ensure their cooling systems perform at their best, keeping their environments comfortably cool throughout the hot summer months.
Refrigerant Leaks
Refrigerant leaks are one of the most common issues found during air conditioning (AC) inspections, especially in warmer climates like Tulsa. Refrigerants are fluids used in air conditioning systems to absorb and transfer heat. They play a crucial role in the cooling process, and without the correct levels, the AC unit cannot operate efficiently. When there’s a leak, not only does it reduce the system’s cooling capacity, but it can also lead to increased energy consumption and higher utility bills as the system works harder to achieve the desired temperature.
Identifying refrigerant leaks can sometimes be challenging because they often occur in hidden lines or connections. AC technicians typically look for signs of leakage such as oil stains or frost build-up on the coils. They may also use specialized tools, such as electronic leak detectors or ultraviolet dye, to find leaks more effectively. Addressing refrigerant leaks promptly is essential for maintaining an AC unit’s health; if left unattended, these leaks can lead to more severe issues such as compressor failure, which can be costly to repair.
In Tulsa, where the demand for reliable air conditioning is high, regular inspections that include checking for refrigerant leaks can save homeowners from unexpected breakdowns and costly repairs. Common problems associated with refrigerant leaks include reduced cooling effectiveness, increased energy costs, and the potential for environmental harm because many refrigerants are greenhouse gases. Therefore, awareness and timely maintenance are key to keeping an AC system running smoothly and efficiently. Regular inspections not only help in detecting refrigerant leaks early but also ensure that the overall air conditioning system remains in optimal working condition, providing comfort during those hot summer months.
Electrical Component Issues
Electrical component issues are a significant concern during air conditioning (AC) inspections, particularly in areas like Tulsa, where extreme seasonal weather changes put additional strain on AC units. These components include a myriad of parts such as capacitors, contactors, wiring, and the compressor itself. Each of these components plays a crucial role in the overall operation of an air conditioning unit, and any malfunction can lead to inadequate cooling, system failure, or even safety risks such as electrical fires.
One common problem found in electrical components is the deterioration of wiring or connections due to age, exposure to moisture, or wear and tear. Over time, wires can corrode or become loose, leading to intermittent power supply issues or even a complete shut down of the AC system. Capacitors are also a frequent point of failure; they provide the necessary start-up energy for the compressor and fan. If a capacitor fails, the system may struggle to start or operate efficiently, resulting in increased energy costs and potential damage to other components due to overheating.
Another concern is the condition of the outdoor unit’s contactor. The contactor is responsible for relaying power to the compressor and the fan. If the contactor is stuck or has burnt connections, it can prevent the AC from functioning properly, leading to a system that does not cool effectively. Regular inspections can catch these issues early on, allowing for preventive measures to avoid costly repairs or replacements down the line.
In Tulsa, where summers can become particularly hot, it is essential to ensure that the electrical components of an AC unit are functioning correctly. During routine inspections, HVAC professionals will check for signs of wear, test electrical connections, and evaluate the overall integrity of the system. Addressing electrical component issues promptly not only helps maintain optimal performance but also prolongs the lifespan of the air conditioning unit, providing peace of mind to homeowners that their system will operate safely and efficiently when they need it most.
Dirty or Clogged Filters
Dirty or clogged filters are one of the most common issues encountered during air conditioning inspections in Tulsa. The air filters in an HVAC system are essential for maintaining clean airflow and ensuring the system operates efficiently. Over time, these filters accumulate dust, allergens, pet dander, and other particulates, which can significantly hinder airflow. When filters are blocked, it forces the system to work harder to pull in air, which can lead to a host of problems.
One of the primary consequences of having dirty or clogged filters is reduced energy efficiency. As the system struggles to push air through a restricted filter, it consumes more energy, which can lead to higher utility bills. Additionally, the increased strain on the AC unit may lead to overheating and potential breakdowns, resulting in costly repairs. Moreover, when the airflow is restricted, the system’s cooling capacity diminishes, leading to discomfort in indoor spaces and failing to adequately cool homes during the hot season.
Another important aspect is how dirty filters can affect the air quality within the home. Poor airflow means that the air in the house isn’t recirculated properly, allowing contaminants to linger. This can exacerbate allergies, respiratory issues, and other health problems for the inhabitants. Regular inspections often reveal the state of the filters and emphasize the importance of routine replacements or cleaning depending on the type of filter used.
In Tulsa, where the summer heat can be intense, maintaining clean filters is even more critical to ensure comfort and efficiency. Homeowners should be proactive in checking their air filters at least once a month, especially during peak usage times. By addressing filter issues promptly, they can enhance air quality, improve energy efficiency, and extend the lifespan of their HVAC systems, ultimately leading to a more comfortable living environment. Regular AC inspections that pay attention to filter conditions can save homeowners time and money while promoting better health and comfort.
Ductwork Problems
Ductwork problems can significantly impact the efficiency and performance of an air conditioning system. The duct system is essential for distributing cooled air throughout a building, and any issues within the ductwork can lead to uneven temperatures, increased energy costs, and reduced comfort for occupants. Common ductwork problems include leaks, blockages, and poor insulation.
Leaks in ductwork can occur due to age, damage, or improper installation. When air escapes through these leaks, it means that less cooled air reaches the intended spaces, forcing the air conditioning system to work harder to maintain desired temperatures. This inefficiency can lead to higher energy bills and increased wear on the AC unit, potentially shortening its lifespan. Additionally, unconditioned air from attics or crawl spaces can enter through leaks, negatively impacting indoor air quality.
Blockages in the ductwork can also create significant issues. Dust, debris, or rodent nests can obstruct airflow, causing the system to strain and potentially leading to overheating. This can trigger safety mechanisms that turn off the system or, in severe cases, can damage the unit itself. Proper maintenance, including regular inspections and cleaning, is essential to prevent these types of blockages and ensure a smoothly operating HVAC system.
Another common issue associated with ductwork is poor insulation. If ductwork runs through unconditioned spaces like attics or basements without proper insulation, the air temperature can change before it arrives at the intended room. This can lead to hot or cold spots within a building and further escalate energy consumption as the system struggles to keep up. For optimal performance, it’s important to ensure that all ductwork is well-insulated, especially in non-conditioned areas.
In Tulsa, where summer heat can be extreme, ensuring that ductwork is in good condition is crucial not only for comfort but also for energy efficiency and indoor air quality. Regular inspections by qualified professionals can help identify ductwork problems before they become serious, ensuring a more reliable and efficient air conditioning system.
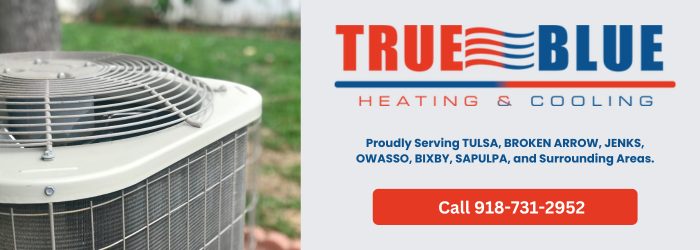
Thermostat Malfunctions
Thermostat malfunctions are one of the most common issues encountered during air conditioning inspections in Tulsa. The thermostat is the control center for the HVAC system, allowing users to set their desired indoor temperature. When it fails, it can lead to a variety of problems, ranging from uncomfortable living conditions to increased energy costs. There are several types of thermostats, including mechanical, digital, and smart thermostats, each susceptible to different issues.
One prevalent problem is incorrect calibration. A thermostat that is not accurately measuring the temperature can cause the air conditioning system to cycle on and off too frequently or not at all. This not only impacts comfort levels but can also lead to unnecessary wear and tear on the system. Additionally, wiring issues—such as frayed wires or connections—can prevent the thermostat from communicating effectively with the air conditioning unit, resulting in inconsistent cooling or no cooling at all.
Another common problem is that older mechanical thermostats may simply fail due to age, causing issues with responsiveness. Even digital and smart thermostats can have software glitches or require new batteries, thus disrupting their function. Furthermore, factors like placement can also affect performance; a thermostat installed in direct sunlight or near drafts can provide inaccurate readings, leading to inefficient system operation. Regular inspections can help identify these issues early, ensuring the HVAC system runs smoothly and effectively, ultimately improving both comfort and energy efficiency in homes throughout Tulsa.