Ductless air conditioning systems, also known as mini-split systems, have become increasingly popular for both residential and commercial settings due to their energy efficiency and versatility. Unlike traditional HVAC systems, ductless AC units offer the flexibility to cool or heat specific areas or rooms without the need for extensive ductwork. While these systems provide significant comfort and convenience, they are not without their challenges. Users may encounter a variety of error codes that can signify potential issues with the unit’s performance or functionality. Understanding these error codes is crucial for homeowners and technicians alike, as it aids in the quick diagnosis and resolution of problems, ultimately prolonging the lifespan of the equipment and ensuring efficient operation.
Error codes are typically designed to convey important information regarding the operational status of ductless AC units. Each manufacturer may have its own set of codes, and these can refer to issues ranging from sensor malfunctions to refrigerant leaks. Some common codes might indicate problems with the outdoor unit, such as overheating or communication failures, while others could point to indoor unit troubles, including blocked filters or fan motor issues. Recognizing what these codes mean enables users to take appropriate action, whether it’s performing simple maintenance tasks or contacting a professional technician for more complex repairs.
As we delve into the world of ductless AC systems, this article will explore some of the most encountered error codes and clarify their meanings. By familiarizing yourself with these indicators, you can enhance your understanding of your air conditioning system, troubleshoot potential issues, and maintain a comfortable indoor environment throughout the year. Understanding these error codes not only empowers users but also leads to more informed decisions regarding maintenance and repair options, saving time and money in the long run.
Common Error Codes for Ductless AC Systems
Ductless air conditioning systems, also known as mini-split systems, are popular for their efficiency and flexibility in climate control. However, like any mechanical system, they can encounter issues that manifest through error codes. Understanding these codes is crucial for diagnosing problems and maintaining the system effectively. Common error codes vary by manufacturer, but some frequent ones include codes related to communications failures, sensor issues, refrigerant problems, and power supply malfunctions.
One of the most common error codes across various brands relates to indoor or outdoor unit communication errors. This typically indicates a problem with the wiring between components or a fault in the control board. Error codes that reference sensor issues often point to temperature or pressure sensors that may have failed or become disconnected, leading to improper functioning of the air conditioning system.
Refrigerant-related error codes might indicate low refrigerant levels due to leaks, which can impair the system’s efficiency and performance. It’s critical to address these issues promptly, as low refrigerant can lead to further damage to the compressor. Additionally, power supply codes often indicate electrical issues that could be caused by circuit overloads or faulty connections, which need immediate attention to ensure safety and prevent system damage.
By interpreting these common error codes accurately, homeowners can take preliminary steps, such as resetting the system or consulting the manual, to troubleshoot their ductless AC systems. This understanding not only helps in managing immediate concerns but also empowers users to engage with technicians more effectively when professional service is required. Identifying these codes is the first step in maintaining a battery of efficient heating and cooling throughout the year and prolonging the lifespan of ductless HVAC systems.
Troubleshooting Steps for Error Codes
When dealing with error codes on ductless air conditioning systems, employing effective troubleshooting steps is crucial to identifying and resolving issues efficiently. A ductless AC system often communicates problems through specific error codes that can vary depending on the brand and model, but there are general steps that can be applied universally.
First, a thorough inspection of the indoor and outdoor units is necessary. Look for visible signs of damage, such as bent fins, blockages in the airflow, or leaks. If the system has a remote or a control panel, you should consult the user manual for definitions of the error codes indicated. This may provide a clear starting point for troubleshooting. Many error codes signify basic issues like filter cleanliness, refrigerant levels, or electrical problems that can be addressed without professional intervention.
Next, check the basic functionality of the unit. This involves verifying that the thermostat is set correctly and functioning properly. Sometimes, an error might simply be the result of user settings or a malfunctioning thermostat rather than a mechanical failure. Cleaning or replacing the air filters can also eliminate common problems associated with error codes, as blocked filters often cause reduced airflow and lead to overheating or underperformance.
If the initial checks don’t resolve the issue, delve deeper into your system’s internals. Inspect the wiring and electrical connections for corrosion, loose connections, or damaged wires. Faulty electrical components can often trigger error codes, and rectifying these issues may restore the system’s operation. Be cautious when handling electrical components; if in doubt about the safety or complexity of the repairs, it may be wise to consult a professional.
Lastly, if the problem persists despite your troubleshooting efforts, it’s advisable to reset the system. This can sometimes clear error codes that are the result of temporary conditions or glitches. Turn off the unit, wait a few minutes, and then turn it back on. If the error code returns, it’s clear that professional assistance is needed to diagnose and repair the underlying problem.
In summary, troubleshooting error codes in ductless AC systems involves a combination of basic inspections, adjusting user settings, checking electrical components, and potentially resetting the unit. Understanding the specifics behind error codes can not only save time but also help in maintaining the overall efficiency and longevity of the air conditioning system.
Manufacturer-Specific Error Codes and Meanings
Ductless air conditioning systems, often referred to as mini-splits, are designed for both efficiency and flexibility in heating and cooling spaces. However, like any complex mechanical system, they can display error codes that indicate malfunctions or issues that require attention. Manufacturer-specific error codes provide essential information that helps users and technicians understand what is wrong with the system. Each manufacturer may have a unique set of codes, which means that the error codes displayed on one brand’s unit may not necessarily translate to another brand.
Understanding these manufacturer-specific error codes is crucial for effective troubleshooting. Often, these codes are accompanied by a brief description in the user manual, detailing the nature of the problem. For example, a common error code could indicate issues related to refrigerant levels, a malfunctioning sensor, or a problem with the indoor or outdoor unit’s electrical components. Knowing the specific error code allows both users and technicians to quickly identify the issue, saving time and reducing the risk of further damage to the system.
In many cases, the error codes inform users when maintenance actions such as filter cleaning or refrigerant checking are needed. Owners should familiarize themselves with their particular model’s error code chart, as it greatly eases the troubleshooting process. Comprehensive user manuals often provide detailed descriptions of each error code, along with recommended actions. For instance, a code indicating a communication issue between the indoor and outdoor units would suggest that the wiring may need inspection or that there might be interference preventing proper communication.
Moreover, understanding these codes not only aids in immediate troubleshooting but also promotes proactive maintenance practices. By recognizing patterns from frequently occurring codes, homeowners can take steps to resolve underlying issues that lead to recurring problems. In conclusion, being aware of and understanding manufacturer-specific error codes can significantly enhance the maintenance and troubleshooting of ductless AC systems, ensuring they operate efficiently and prolonging their lifespan.
Preventative Measures to Avoid Error Codes
To maintain the optimal performance of ductless AC systems and minimize the frequency of error codes, implementing preventative measures is essential. Regular maintenance is a cornerstone of this proactive approach. It includes routine checks, cleanings, and necessary repairs that can help identify potential issues before they escalate into significant problems. Dust and debris can accumulate in the air filters, coils, and drain lines, leading to reduced efficiency and potential malfunction. Therefore, homeowners should clean or replace air filters every few months and ensure the outdoor unit is free from obstructions.
Another crucial aspect of preventative measures is ensuring proper installation and settings of the ductless AC system. If the unit is incorrectly sized or not installed according to the manufacturer’s specifications, it may operate inefficiently and trigger error codes. Engaging professional installers familiar with ductless systems gives homeowners peace of mind knowing that the installation is correct, which can prevent future issues associated with air flow or refrigerant levels.
Regular inspections of the electrical components and refrigerant levels also play a vital role in preventing error codes. If there is an electrical malfunction, such as loose wiring or a failing capacitor, it may manifest as an error code. Scheduled professional inspections can help detect electrical issues early. Moreover, ensuring the refrigerant levels are within the manufacturer’s recommended range is critical. Low refrigerant levels can lead to system strain and efficiency loss, resulting in error codes.
Lastly, providing consumption awareness can help mitigate operational problems. Educating users on the appropriate settings and operation of their ductless AC units can also contribute to smoother functioning. For instance, frequent changing of temperature settings or overworking the unit can lead to wear and tear, which can subsequently trigger error codes. By combining these preventative measures, homeowners can enhance the longevity and reliability of their ductless AC systems while significantly reducing the risk of encountering error codes.
In summary, taking proactive steps such as regular maintenance, professional installation, electrical inspections, and proper usage of the ductless AC system can greatly reduce the likelihood of error codes occurring. It is much easier to prevent errors than to troubleshoot after a code appears, making these measures essential for homeowners looking to maintain their ductless air conditioning systems efficiently.
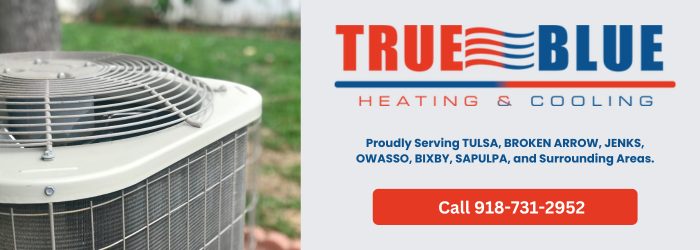
When to Seek Professional Help for Error Codes
Ductless air conditioning systems are designed to operate independently and efficiently. However, like any mechanical device, they can experience issues which may trigger various error codes. Understanding when to seek professional help is crucial in ensuring the longevity of your ductless AC system and maintaining its efficient operation.
If you encounter an error code that persists despite following basic troubleshooting steps, it is a clear indication that professional intervention is necessary. For instance, if your unit continues to display an error code after you’ve reset it, checked the filters, or ensured proper refrigerant levels, this points to a deeper issue that may involve the internal components of the system. Furthermore, if you are uncertain about the error code’s meaning or how to carry out further troubleshooting, it is advisable to consult a professional who can provide expert insights and accurate diagnostics.
Additionally, certain symptoms may signal an urgent need for professional assistance. Signs such as unusual noises, inconsistent temperature output, refrigerant leaks, or a significant drop in system performance are not only indicators of potential underlying problems but can also lead to more extensive damage if left unaddressed. In such cases, it is better to err on the side of caution and contact a certified technician to inspect the unit and perform necessary repairs. Doing so will not only ensure that the problem is resolved appropriately but can also prevent further complications and expenses down the line.
In conclusion, while some error codes and issues might be manageable through DIY methods, others necessitate the expertise of a professional. A proactive approach in recognizing when to seek help can save you time, reduce repair costs, and extend the lifespan of your ductless AC system. Always prioritize safety and efficiency by ensuring any complex or persistent issues are handled by trained professionals.