When it comes to maintaining a comfortable indoor environment, a well-functioning air conditioning (AC) system is essential, especially during the sweltering summer months. Conducting regular AC inspections is a proactive measure that can lead to improved performance, increased energy efficiency, and a longer lifespan for your cooling unit. However, not all inspections are created equal, and homeowners must be vigilant about potential red flags that can signal underlying issues. Identifying these warning signs early can prevent costly repairs down the line and ensure that your AC system operates smoothly throughout its service life.
During an AC inspection, technicians may uncover various problems that could affect system performance. These red flags often manifest in changes to airflow, unusual noises, or even unpleasant odors emanating from the unit. Understanding these indicators is crucial for homeowners, as they can be the first step in addressing issues before they escalate. Additionally, recognizing these signs not only aids in the immediate maintenance of the air conditioning system but also empowers homeowners to engage more effectively with service technicians, ensuring that any necessary repairs or services are identified and completed in a timely manner.
In this article, we will delve into the key red flags to watch out for during AC inspections, offering insights into what they mean and how they can impact the reliability and efficiency of your cooling system. By equipping yourself with knowledge about these potential issues, you can take an active role in the upkeep of your AC unit, ensuring a comfortable living space and peace of mind throughout the heating and cooling seasons. Whether you’re a seasoned homeowner or new to property maintenance, understanding these warning signs will help you navigate the complexities of AC maintenance with confidence and clarity.
Inconsistent Temperature Readings
Inconsistent temperature readings during an air conditioning (AC) inspection can be a significant indicator of underlying issues within the system. When a thermostat fails to maintain a consistent temperature, or when different areas of a space experience varying comfort levels, it suggests that the AC unit may not be functioning optimally. This inconsistency can arise from numerous factors, including malfunctioning thermostats, blocked air filters, or improper refrigerant levels. Each of these issues can lead to inefficiencies, resulting in discomfort and potentially escalating energy costs.
One of the first areas to check when encountering inconsistent temperature readings is the placement and function of the thermostat. If the thermostat is located in a drafty area or near a heat source, it may produce inaccurate readings, causing the AC unit to overwork or underperform. Additionally, dirty or clogged air filters can restrict airflow, leading to hot spots in the home where the air conditioning cannot reach. Periodic maintenance and filter changes are crucial for ensuring consistent airflow and performance.
Another critical aspect to consider is the overall health of the refrigerant levels. An improper level can lead to insufficient cooling performance, resulting in varying temperatures throughout the space. If low refrigerant levels are detected, it may indicate a refrigerant leak, which needs to be addressed. Regular inspections by a qualified technician can help identify these problems early on, ensuring the AC unit operates efficiently and prolonging its lifespan.
When it comes to AC inspections, there are various red flags to watch for that can indicate problems. Beyond inconsistent temperature readings, it’s important to pay attention to unusual noises or odors, which could signify deeper mechanical issues. Regular monitoring of these signs can lead to timely interventions and repairs, ultimately leading to a more comfortable indoor environment and lower energy bills. Overall, addressing these red flags during an AC inspection can not only rectify immediate issues but also prevent future complications that could arise from neglecting these warning signs.
Unusual Noises or Odors
During an air conditioning (AC) inspection, encountering unusual noises or odors is a significant red flag that should not be overlooked. Typically, an AC unit operates quietly, producing only the soft sound of air flowing through the ducts and the gentle hum of the compressor. However, if you notice sounds like banging, hissing, clanking, or grinding, it’s a clear indication that something is amiss. These noises can stem from a variety of issues, such as loose components, debris obstructing parts of the unit, or even more serious mechanical failures. For instance, a grinding noise could suggest that the motor bearings are wearing out, while a hissing sound might indicate a refrigerant leak.
In addition to unusual noises, unpleasant odors can also signal problems that need immediate attention. A musty smell may indicate mold or mildew buildup in the system, which can lead to health issues and reduced air quality. A burning smell could be a sign of electrical issues within the unit, while a sweet, chemical-like odor might suggest refrigerant leaks, particularly with certain types of refrigerants that carry a distinct scent. Addressing these smells promptly is essential to prevent further damage to the unit and ensure the safety of the occupants in the building or home.
When unusual sounds and odors are present, it’s crucial to take them seriously and have a qualified HVAC technician perform a thorough inspection. They will be able to diagnose the source of the problem and recommend appropriate repairs or maintenance solutions. Ignoring these signs can lead to more extensive and costly repairs down the line, as well as compromise the efficiency and longevity of your AC system. Regular maintenance and prompt attention to any irregularities can help ensure your air conditioning unit operates smoothly and reliably.
Refrigerant Leaks
Refrigerant leaks are a significant concern during air conditioning (AC) inspections, as they can negatively impact the efficiency and functionality of the cooling system. Refrigerant is a crucial component in the air conditioning cycle, facilitating the absorption and release of heat to cool the space effectively. A leak not only diminishes the system’s performance but can also lead to higher energy bills and increased wear on other components as the system struggles to maintain the desired indoor temperature.
Identifying refrigerant leaks during an inspection involves looking for various indicators. Common signs include ice buildup on the evaporator coils, hissing or bubbling sounds, and a noticeable decrease in cooling efficiency. Additionally, technicians may use special detection devices or ultraviolet dye to pinpoint leaks that may not be immediately visible. Addressing refrigerant leaks promptly is crucial, as operating an AC unit with low refrigerant can lead to compressor failure, which is often one of the most expensive components to replace.
When it comes to the potential dangers associated with refrigerant, there are also environmental and health considerations. Many refrigerants used in residential AC systems are considered greenhouse gases, and leaks can contribute to environmental harm. Some refrigerants can be harmful if inhaled or if they come into contact with skin, making it essential to have any leaks professionally repaired. Regular inspections can help catch these issues early, ensuring not only the longevity and efficiency of the AC system but also the health and safety of its occupants. Overall, vigilance regarding refrigerant levels and prompt action regarding leaks are key components of maintaining an effective air conditioning system.
Electrical Issues or Warning Signs
Electrical issues or warning signs during an air conditioning (AC) inspection can be critical indicators of underlying problems that could compromise the system’s performance and safety. These issues may manifest in various forms, including tripped circuit breakers, flickering lights when the AC unit operates, or the presence of burnt smells coming from the unit or its wiring. Each of these red flags warrants immediate attention, as they not only affect the efficiency of the cooling system but could pose serious electrical hazards as well.
One common electrical issue observed during inspections is the failure of contactors or relays. These components manage the power supply to the AC unit, and when they malfunction, it can lead to an inability to start the system or, conversely, cause it to overrun and draw excessive power. Additionally, a failing capacitor can also produce warning signs, often resulting in difficulties in starting the compressor or producing cooling. Inspectors should also be vigilant for signs of poor wiring practices or degraded insulation on electrical cables, which can increase the risk of short circuits or fires.
Another key element to consider during an inspection is the efficiency of the electrical connections. Loose or corroded wiring can lead to poor electrical conductivity, causing increased resistance, overheating, and eventual system failure. Frequent circuit tripping can indicate that the AC is drawing more power than it should, possibly due to an electrical issue. Inspectors should also check the breaker box to ensure that the electrical supply matches the system’s required specifications. If any discrepancies are noted, they may signify the need for upgrades or repairs to meet safety standards and ensure optimal operation.
In summary, electrical issues in air conditioning systems can present serious risks and should never be overlooked during inspections. Recognizing the warning signs early on can not only prevent costly repairs but can also ensure the safety and efficacy of the cooling system. Regular maintenance, along with diligent inspections, will help in identifying and addressing these electrical issues, thereby extending the lifespan of the AC unit and maintaining a comfortable environment.
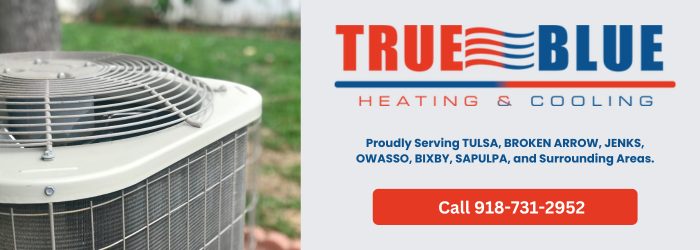
Wear and Tear on Components
During an air conditioning (AC) inspection, one of the primary concerns is the wear and tear on various components of the system. Over time, AC units experience regular use, which can lead to degradation of parts such as the compressor, fan blades, coils, and ductwork. These components are critical to the efficient operation of the air conditioning system, and any signs of wear can significantly impact performance, energy efficiency, and the longevity of the unit.
Inspecting for wear and tear typically involves checking for rust, corrosion, cracked or frayed wires, and worn-out belts or bearings. For instance, an aging compressor may struggle to maintain temperature, leading to increased energy consumption and higher utility bills. Similarly, fan blades that are bent or damaged can disrupt airflow, leading to inefficient cooling and potential overheating of other components. Additionally, ductwork that has become degraded can result in leaks, wasting valuable conditioned air and reducing overall efficiency.
It’s essential to address wear and tear issues promptly. Ignoring these signs can result in more severe problems down the line, including costly repairs or even the need for a complete unit replacement. Regular maintenance and inspection will help identify these issues early, allowing for the appropriate corrective actions to be taken before they escalate.
When it comes to AC inspections, red flags to watch out for include not only visible signs of wear and tear but also irregular performance characteristics. For example, if the system is running but struggling to maintain the desired temperature, it may indicate underlying wear in the components. Additionally, if the unit is cycling on and off frequently, this could suggest that critical components are under undue strain due to wear. Being attentive to these indicators can help homeowners maintain their air conditioning systems effectively, ensuring optimal performance and comfort in their living spaces.