Diagnosing electrical problems in air conditioning (AC) compressors is a crucial skill for HVAC technicians, especially in regions like Tulsa, where the summer heat can be relentless and a malfunctioning AC system can render living and working environments uncomfortable. The complexity of modern AC systems, combined with the high demand for reliable cooling solutions in such climates, necessitates a thorough understanding of both mechanical and electrical components. The compressor, known as the heart of the AC system, plays a pivotal role in circulating refrigerant and maintaining optimal temperatures. Therefore, identifying electrical issues within this component is essential for effective problem resolution.
In Tulsa, where temperatures can soar, homeowners and businesses alike rely heavily on their AC systems to provide relief from the heat. However, various electrical problems—ranging from faulty wiring and blown fuses to issues with capacitors and contactors—can impede the compressor’s operation, leading to inefficient cooling or complete system failure. An accurate diagnosis not only improves the performance and longevity of the AC unit but also saves time and money in repair costs. Thus, understanding the common signs of electrical problems and the diagnostic steps involved can empower technicians and homeowners alike to take swift and informed action.
This article aims to provide a comprehensive guide on how to diagnose electrical problems in AC compressors specifically tailored for Tulsa’s unique climate and challenges. We will discuss the common symptoms of electrical malfunctions, the necessary tools for efficient diagnosis, and the systematic approach to identifying and resolving issues. By equipping readers with practical knowledge and insights, we hope to enhance their ability to maintain a functional and dependable air conditioning system, ensuring comfort throughout the hottest months of the year.
Common Symptoms of AC Compressor Issues
When dealing with air conditioning systems, particularly with the compressor, it’s crucial to recognize the common symptoms that indicate potential issues. The AC compressor is a vital component responsible for circulating the refrigerant necessary for cooling the indoor air. Understanding the warning signs can help in early diagnosis and prevent further damage to the system.
One of the most prevalent symptoms of AC compressor issues is unusual noises. If the compressor is making grinding, clicking, or clinking sounds, it could indicate that there are internal components rubbing against each other or that there are loose parts. Additionally, if the compressor is struggling to start or frequently cycling on and off, this could be a sign of electrical problems or that the compressor is beginning to fail. High energy bills can also be a symptom; if the AC compressor is working harder than it should due to underlying issues, it can draw more power, leading to inflated energy costs.
Another significant sign of potential trouble is a lack of cool air being emitted from the vents. When the compressor is malfunctioning, it may not be able to effectively compress the refrigerant, leading to inadequate cooling. It is also important to pay attention to temperature fluctuations or inadequate cooling, which may suggest that the compressor is not functioning efficiently.
Diagnosing electrical problems specifically in AC compressors in Tulsa is a critical task that combines observation and systematic testing. First, visual inspections should be conducted to check for any signs of overheating, burnt wires, or melted components. Assessing the wiring and electrical connections is essential, as loose, corroded, or damaged connections can lead to a variety of electrical failures.
After conducting a visual inspection, technicians should use appropriate diagnostic tools such as multimeters to measure voltage and current flowing through the compressor. This is essential for identifying any irregularities in the power supply or checking for overload conditions. These measurements can help pinpoint whether the issue resides within the compressor itself or in the electrical circuitry feeding it. Additionally, examining fuses and relays for continuity is necessary to ensure they are functioning correctly and not contributing to the compressor’s failure.
In Tulsa, where the climate can put a strain on HVAC systems, identifying these electrical issues early can save homeowners from costly repairs and ensure efficient operation during hotter months. Regular maintenance, combined with knowledge of common symptoms and systematic diagnostic approaches, can keep AC systems running smoothly and effectively.
Tools and Equipment for Diagnosis
Diagnosing electrical problems in AC compressors, particularly in a climate such as Tulsa’s, requires a variety of tools and equipment. A systematic approach starts with the right diagnostic tools, which aid in pinpointing issues effectively and efficiently. Essential tools include digital multimeters (DMM), which are used to measure voltage, resistance, and current, providing a clear picture of the electrical health of the compressor. Clamp meters are also invaluable; they allow technicians to measure current flow without needing to disconnect any wires, making diagnosis safer and simpler.
Another vital tool is a set of pressure gauges. These gauges help in assessing refrigerant pressures to ensure that the compressor is functioning under optimal conditions. Low or high pressures may indicate underlying problems that could correlate with electrical issues. Additionally, using an oscilloscope can help visualize the electrical signals and waveforms, which is crucial for more advanced diagnostics. It can reveal inconsistencies in current flow that may not be observable with simpler tools.
In terms of equipment, having a reliable set of screwdrivers, wrenches, and pliers is fundamental, as they allow for opening up the compressor and inspecting internal components. Insulation resistance testers can also be employed to check for shorts or insulation failures, ensuring that electrical currents are contained within their intended pathways. Furthermore, specialized tools like refrigerant reclaimers and vacuum pumps may be necessary if refrigerant levels must be managed during the diagnosis process.
When diagnosing electrical problems specifically, knowledge of the AC system layout and electrical schematics is crucial. This understanding enables technicians to trace wires, locate potential fault points, and perform tests in the necessary sequences. Combined, these tools and equipment allow for a thorough analysis, ensuring reliable assessments and repairs of AC compressors, ultimately leading to better performance and longevity of the equipment. In a place like Tulsa, where summers can be swelteringly hot, efficient AC operation is vital for comfort and safety, making the proper diagnosis crucial for homeowners and technicians alike.
Electrical Circuit Analysis and Testing
When diagnosing electrical problems in AC compressors, conducting a thorough electrical circuit analysis and testing is crucial. This process involves examining the various components of the AC system, including power supply, control circuits, and safety devices, to identify any faults or malfunctions that may prevent the compressor from operating effectively.
To start with electrical circuit analysis, it’s important to have a clear understanding of the compressor’s wiring diagram. This diagram will provide essential information about how the different components are connected, allowing technicians to trace the electrical pathways and identify any potential issues. Technicians typically begin by checking for proper voltage at the compressor terminals, ensuring that it is receiving the correct power supply. If the voltage is low or absent, it may indicate issues such as a blown fuse, tripped breaker, or problem with the electrical supply source.
Once the power supply is confirmed, continuity testing can be performed on the compressor’s windings and other connected components. This involves using a multimeter to measure resistance and ensure that there are no open circuits or shorts present. Inspecting the contactor or relay involved in the compressor’s operation is also critical, as these components are responsible for switching the power to the compressor. Any signs of burnt contacts or wear could prevent proper operation.
Using an oscilloscope or clamp meter can further enhance the analysis, allowing technicians to observe the waveform of the electrical signals and diagnose issues such as current imbalance or harmonics that might stress the compressor’s electrical components. By performing a systematic electrical circuit analysis and testing, technicians in Tulsa can pinpoint specific faults in the AC compressor system and develop effective repair strategies to restore proper functionality. Proper diagnosis not only improves the likelihood of a successful repair but also contributes to the longevity and efficiency of the AC system overall.
Troubleshooting Techniques for AC Compressors
When it comes to diagnosing electrical problems in AC compressors, effective troubleshooting techniques are essential. The first step in troubleshooting is to observe any common symptoms of AC compressor issues, such as unusual noises, failure to start, or inconsistent cooling performance. These signs can give a technician valuable clues regarding where to begin the diagnosis. Visual inspection plays a critical role in this stage; this includes checking for visible wear and tear, loose connections, or burnt wires, which may indicate a larger problem within the compressor’s electrical system.
Another important troubleshooting technique is the use of diagnostic tools and equipment to test various components of the AC compressor. Multi-meters are invaluable for checking voltage levels and continuity in electrical circuits. When testing the compressor’s start relay and capacitor, a technician must ensure that the components are functioning correctly. Low voltage readings or open circuits can point to the possibility of faulty components that need to be replaced. In addition, employing clamp meters can help measure the amperage being drawn by the compressor, providing insight into its operational health. An excessively high current draw can signify electrical overload or a failing compressor.
Once initial tests are completed, the technician should analyze the readings against the specifications outlined in the system’s documentation. Comparison of these results allows for a better understanding of whether the issues stem from the electrical components or if they are caused by external factors, like refrigerant levels or airflow restrictions. It is also crucial to follow a systematic approach when isolating potential causes. For instance, if the compressor is not engaging, check if the thermostat is calling for cooling, and ensure the system’s safety switches are not tripped. If power is present and the system still doesn’t function, then faulted internal components may be at play.
Diagnosing AC compressor electrical problems in Tulsa requires not only technical knowledge but also a methodical approach. Technicians may encounter various brands and models with different specifications, which they must be familiar with to effectively troubleshoot. Therefore, ongoing education and experience are invaluable in developing the skill set needed to handle these complex systems efficiently. Putting these techniques into practice can lead not only to a successful diagnosis but also to a more effective resolution of issues, returning the AC system to optimal functionality.
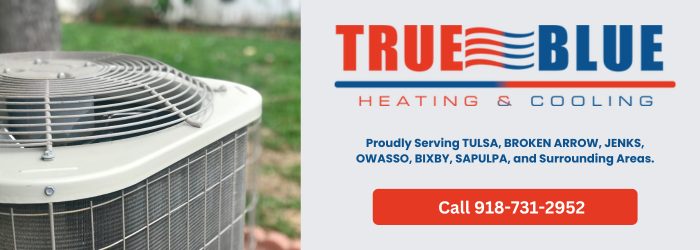
Safety Precautions During Diagnosis
When diagnosing electrical problems in AC compressors, safety is of utmost importance. The electrical components in air conditioning systems carry high voltage and can pose serious risks including electric shock or burns. Therefore, it is essential to follow certain safety precautions to ensure both the technician’s safety and the integrity of the HVAC system.
First and foremost, always disconnect power to the AC unit before starting any diagnostic procedures. This involves turning off the circuit breaker that supplies electricity to the compressor, which helps to prevent accidental energization while you’re working on the unit. It is also wise to use a lockout/tagout procedure, which involves placing a physical lock on the circuit breaker to prevent it from being turned back on accidentally.
Additionally, wearing appropriate personal protective equipment (PPE) is vital. Technicians should wear insulated gloves and safety glasses to protect themselves from electric shocks and flying debris. It is also advisable to stand on an insulated mat when working near electrical components to reduce the risk of electric shock. Furthermore, ensuring that your tools are in good condition and that you are using insulated tools can help minimize risks.
Remaining aware of your surroundings is another key aspect of safety. Be conscious of the possibility of slippery surfaces or obstacles near the AC unit that could lead to falls. It is also advisable to work in pairs when taking on major repairs, especially when diagnosing high-voltage systems. Having a second person nearby can provide assistance in case of emergencies.
In summary, safety precautions during diagnosis of AC compressors are crucial. By disconnecting power, using proper PPE, ensuring tools are safe for use, and staying vigilant about your surroundings, you can significantly reduce the risk of accidents. Always prioritize safety, as it allows for a more thorough and worry-free diagnostic process, ultimately leading to effective repairs and maintenance of the AC system.