Air conditioning systems play a crucial role in maintaining a comfortable indoor environment, especially during the sweltering summer months. While many property owners understand the importance of regular air conditioning inspections, the complexities and requirements can vary significantly between residential and commercial properties. Commercial properties, which encompass everything from office buildings and retail spaces to warehouses and manufacturing facilities, often operate on a larger scale and require more nuanced considerations when it comes to HVAC systems. Thus, an understanding of how AC inspections differ in commercial properties is essential for business owners, property managers, and facility maintenance personnel.
One of the primary distinctions in AC inspections for commercial properties lies in the scale and complexity of the systems involved. Commercial HVAC systems are typically larger and more intricate than their residential counterparts, often designed to accommodate higher cooling loads and provide climate control for multiple zones or floors. This complexity necessitates specialized inspection protocols that take into account various components such as chillers, cooling towers, air handling units, and sophisticated ductwork. Furthermore, commercial inspections are often mandated by industry regulations and standards, which can vary based on the type of business and local codes. Understanding these regulatory requirements is critical for compliance and operational efficiency.
Additionally, the frequency and depth of AC inspections differ significantly between residential and commercial settings. While a homeowner might schedule seasonal maintenance, commercial properties often require more regular and thorough inspections due to the continuous operation of their HVAC systems and the potential impact on business operations. These inspections not only ensure optimal performance and energy efficiency but also help identify potential issues that could lead to costly downtime or equipment failure. The proactive management of HVAC systems in commercial properties is vital, as an inefficient or malfunctioning system can directly affect employee productivity, customer comfort, and overall business reputation.
In this article, we will explore these differences in detail, examining the key factors that influence AC inspections for commercial properties and highlighting best practices to ensure that these essential systems operate at peak efficiency. Whether you are a property manager, business owner, or service technician, understanding these distinctions will equip you with the knowledge necessary to maintain optimal air conditioning solutions that meet the unique demands of commercial environments.
Types of HVAC Systems in Commercial Properties
In commercial properties, the types of HVAC (Heating, Ventilation, and Air Conditioning) systems used can significantly differ from those found in residential settings due to the scale, complexity, and unique requirements of such buildings. Commercial HVAC systems are designed to handle larger spaces, more occupants, and more complex layouts than those typically seen in homes. The most common types of HVAC systems used in commercial properties include packaged systems, split systems, and centralized systems.
Packaged systems are often situated on the roof and combine heating and cooling components in one unit, making them ideal for commercial buildings with limited interior space. These systems are efficient for larger facilities as they distribute air through ducts to various parts of the building. Split systems, on the other hand, have separate indoor and outdoor units that work together to provide climate control. This setup is more flexible and can efficiently serve different areas within a larger facility, allowing for tailored climate control.
Centralized systems are typically employed in larger commercial buildings, providing a single point for heating and cooling, which then distributes conditioned air through a network of ducts. These are often integrated with sophisticated controls, allowing for greater energy efficiency and better management of the indoor environment. The complexity of these systems means that they require thorough and regular inspections to ensure they operate efficiently and comply with safety regulations.
When it comes to how AC inspections differ for commercial properties compared to residential ones, there are several key factors at play. First, commercial inspections must adhere to stricter compliance regulations and safety codes, given the higher occupancy and utilization of the structures. The increased load and use in commercial systems also means that inspections might delve deeper into components like refrigerants, cooling towers, and air handling units, which may not be present in residential settings.
Additionally, commercial HVAC systems typically operate under heavier use conditions, which can exacerbate wear and tear, leading to a greater need for regular maintenance and inspections. Factors such as the size of the facility, the number of employees, and the variety of equipment in use necessitate a more rigorous inspection process. This can involve checking for mechanical failures, ensuring efficient operation, and verifying that air quality standards are met in spaces where large groups of people congregate.
Overall, the complexity and variety of HVAC systems found in commercial properties require specialized knowledge during inspections, ensuring the systems function optimally and maintain safety standards. Regular inspections not only promote energy efficiency but also help in preventing costly repairs and ensuring a comfortable environment for occupants.
Regulatory and Compliance Requirements
Understanding the regulatory and compliance requirements for air conditioning (AC) inspections in commercial properties is crucial for maintaining legal operation and ensuring the safety and comfort of occupants. These requirements vary by location and are often dictated by state and local laws, as well as by industry standards. Compliance not only pertains to ensuring that equipment meets certain performance standards but also involves adhering to environmental regulations, health codes, and safety protocols.
In many regions, commercial properties are subject to specific codes that require regular inspections of HVAC systems to ensure they function efficiently and do not pose health risks to employees or customers. For instance, the Environmental Protection Agency (EPA) sets forth regulations regarding refrigerants used in cooling systems, necessitating that businesses adhere to practices that prevent leaks and manage environmental impact. Moreover, the Occupational Safety and Health Administration (OSHA) enforces guidelines ensuring that workplace environments are safe, which encompasses proper ventilation and temperature control provided by HVAC systems.
Additionally, commercial buildings may be required to demonstrate energy efficiency, which has led to the incorporation of standards like ASHRAE (the American Society of Heating, Refrigerating and Air-Conditioning Engineers) guidelines. These guidelines not only establish baseline performance expectations but also serve to inform audit and inspection procedures. Failure to comply with these regulations can result in hefty fines, legal action, and an increased risk of HVAC system failure, which can disrupt business operations and affect tenant satisfaction.
Inspections typically involve reviewing documentation to ensure previous compliance with regulations and assessing the physical condition of the AC systems against mandated standards. By identifying deficiencies during inspections, property managers can not only avoid potential penalties but also take proactive steps to improve system performance, ultimately reducing operational costs and enhancing overall safety and comfort within the facility. Thus, comprehensively understanding and navigating the complex web of regulatory and compliance requirements is essential for effective AC management in commercial settings, promoting not just legal adherence but also operational excellence.
Frequency and Scheduling of Inspections
The frequency and scheduling of air conditioning (AC) inspections in commercial properties is a vital aspect of maintaining optimal operational efficiency and compliance with regulations. Unlike residential properties, where inspections might occur annually or biannually, commercial properties often require more frequent evaluations due to their complex systems and higher usage demands. The specific frequency can vary significantly based on several factors, including the type of business, the size of the equipment, and the volume of use. For instance, businesses that operate under stringent health and safety regulations, such as hospitals or food service establishments, often necessitate inspections on a quarterly basis or even more frequently.
Scheduling these inspections is also crucial, as it must align with the operational hours of the business to minimize disruption. For many commercial entities, inspection schedules are set up in off-peak hours or during maintenance downtimes to ensure that the flow of business remains uninterrupted. Additionally, regular inspections help identify potential issues before they escalate into costly repairs or operational downtime, which can severely impact business continuity.
Another element to consider is that some commercial properties may be subject to specific contracts with their HVAC service providers that dictate the minimum frequency of inspection. This is often negotiated to tailor to the unique needs of the business, ensuring that the HVAC systems operate efficiently under varying conditions. Furthermore, seasonal changes can dictate the need for inspections; for instance, before summer hits, buildings might require a thorough checkup of their cooling systems to prepare for the heightened demand.
In summary, while the specifics of frequency and scheduling may vary among different commercial properties, the common goal remains the same: to ensure that HVAC systems run effectively and efficiently to provide a comfortable environment for occupants while adhering to regulatory requirements. Regular inspections not only promote better performance and energy efficiency but also significantly extend the lifespan of the HVAC units, yielding long-term savings for the business.
Specific Inspection Criteria for Commercial Units
When it comes to the specific inspection criteria for commercial air conditioning (AC) units, the process is generally more complex than that of residential systems. Commercial properties often have larger and more intricate HVAC systems that require tailored inspection protocols. Each type of commercial unit may have unique components, such as rooftop units, modular chillers, or multi-zone systems, that necessitate a thorough evaluation of their operational performance, efficiency, and regulatory compliance.
Commercial AC inspections typically begin with a comprehensive evaluation of the unit’s physical condition. Inspectors will examine external components like condenser coils, fans, and electrical connections for any signs of wear or damage. Additionally, they will assess internal components, including filters, ducts, and drain pans, for cleanliness and operational efficiency. This can include checking for clogs in drainage systems that might lead to water damage or mold growth, a crucial concern in larger commercial buildings where maintenance may not be as frequent.
Another critical aspect of the inspection criteria is ensuring that the HVAC system operates at peak efficiency. This involves evaluating the system’s energy consumption and checking it against industry standards to identify any potential inefficiencies or areas for improvement. Inspectors will often review maintenance logs and service records to ensure that routine upkeep has been performed adequately, as neglecting regular maintenance can lead to larger, more expensive issues down the line.
Moreover, the inspection of commercial HVAC systems often includes verifying compliance with local codes, environmental regulations, and industry standards. This may involve checking refrigerants and ensuring that they meet regulations regarding ozone-depleting substances. Non-compliance can lead to substantial fines and operational disruptions, making it critical to adhere to these guidelines during inspections.
Ultimately, the specific inspection criteria for commercial units are designed not only to meet regulatory requirements but also to ensure the longevity and efficiency of HVAC systems. Such thorough inspections can prevent costly breakdowns and enhance indoor air quality, providing a comfortable and safe environment for employees and clients alike. Given the significant investment commercial properties make in their HVAC systems, consistent vigilance in inspection practices is essential to safeguard that investment and maintain operational efficiency.
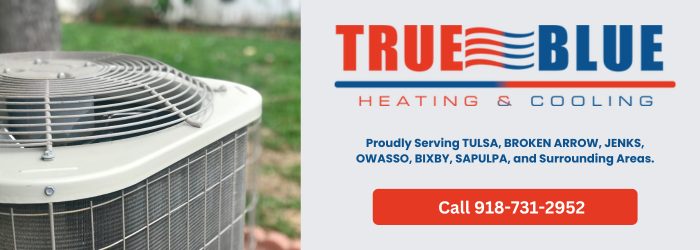
Impact of Building Size and Usage on Inspection Protocols
The inspection protocols for air conditioning systems in commercial properties are significantly influenced by the size and usage of a building. Larger buildings, such as skyscrapers or expansive office complexes, may require more comprehensive inspection protocols due to their complex HVAC systems and the diverse environments within. For instance, a high-rise office building with multiple floors would have distinct HVAC needs on different levels, necessitating tailored inspection measures for each zone to ensure optimal performance and energy efficiency.
The usage of a building also plays a critical role in determining inspection frequency and requirements. Buildings that accommodate large gatherings of people, such as theaters, conference centers, or schools, are exposed to different levels of wear and tear on their HVAC systems compared to smaller, less frequented establishments. High-occupancy buildings generate more heat and humidity, leading to increased demand on air conditioning systems. Therefore, these systems must be inspected more frequently to avoid breakdowns and to maintain a comfortable environment, which is vital for the health and productivity of occupants.
Moreover, the nature of the building’s use can impact the types of inspections performed. For example, a laboratory or manufacturing facility may have stricter air quality and ventilation requirements due to the presence of hazardous materials or specialized processes, thus requiring inspections that focus on environmental safety and compliance with specific health regulations. In contrast, a standard office building might prioritize inspections that focus more on general operational efficiency and comfort for its occupants.
In summary, when considering AC inspections for commercial properties, both the size of the building and its intended use are paramount. These factors dictate not only the frequency of inspections but also the specific criteria and protocols that must be adhered to in order to safeguard the building’s functionality and the well-being of its users. Effective inspection practices that account for these variables ensure that HVAC systems operate at peak performance, thereby enhancing energy efficiency and building compliance.