In the realm of home maintenance, few systems are as integral to comfort and health as the air conditioning (AC) system. As temperatures rise and indoor climates become more crucial for well-being, ensuring that these systems operate efficiently is paramount. However, many homeowners overlook the importance of regular AC inspections, which serve not just as routine checks but as a proactive measure to identify potential future problems. By understanding how thorough inspections can unveil underlying issues, homeowners can save on potentially costly repairs, enhance energy efficiency, and prolong the lifespan of their HVAC systems.
AC inspections encompass a comprehensive evaluation of the various components that contribute to the system’s functionality, including the compressor, evaporator coils, ductwork, and refrigerant levels. Trained technicians methodically assess each element, looking for signs of wear and tear, inefficiencies, and other indicators that may suggest looming issues. These proactive inspections help detect anomalies before they escalate into significant malfunctions, thereby ensuring that the system operates at optimal performance levels. This preemptive strategy not only safeguards indoor comfort but also stands to reduce energy expenditures by ensuring the system runs efficiently.
Furthermore, regular inspections have implications beyond immediate savings; they play a crucial role in maintaining air quality and comfort levels. An AC system that is not functioning optimally can circulate pollutants, allergens, and humidity, potentially jeopardizing the health of occupants. Through inspections, technicians can also evaluate the cleanliness of filters and ducts, which contribute significantly to indoor air quality. By addressing these concerns early, homeowners can create a healthier living environment while preventing further deterioration of the AC system.
In summary, AC inspections are invaluable tools in a homeowner’s maintenance arsenal. They serve as a bridge between routine care and the long-term vitality of the air conditioning system, enabling homeowners to enjoy uninterrupted comfort while avoiding the pitfalls of unexpected repairs. In the following sections, we will delve deeper into the specific ways in which AC inspections can unearth potential problems, the benefits of staying ahead of issues, and practical steps homeowners can take to ensure their systems remain in peak condition.
Early Detection of Refrigerant Leaks
Early detection of refrigerant leaks is a critical aspect of air conditioning (AC) inspections that can significantly influence both the efficiency and longevity of the system. Refrigerant plays a crucial role in the cooling process by absorbing heat from the indoor air and releasing it outside. When there is a leak, the refrigerant levels drop, leading to diminished cooling capacity and increased energy consumption as the system struggles to maintain the desired indoor temperature. Consequently, this not only impacts comfort levels but also results in higher utility bills and potential damage to the compressor due to overheating.
During an AC inspection, trained technicians will employ specialized tools and methods to identify any signs of refrigerant leaks. This may include visual inspections for oil stains around refrigerant lines and connections, as refrigerants often carry oil that leaks with them. Technicians may also use electronic leak detectors or bubble solutions to pinpoint leaks effectively. Early detection is crucial because it allows homeowners to address the issue promptly, preventing more severe complications down the line, such as complete system failure or a need for costly repairs or replacement.
Furthermore, addressing refrigerant leaks early can also contribute to environmental conservation. Many refrigerants, particularly older types, have been found to contribute to global warming and ozone depletion. By ensuring that an HVAC system operates with the appropriate amount of refrigerant, homeowners not only enhance their comfort but also play a part in reducing harmful emissions. Regular AC inspections that include checks for refrigerant leaks thereby serve both economic and environmental interests, emphasizing their importance in home maintenance and sustainability efforts.
In summary, early detection of refrigerant leaks during AC inspections is essential for maintaining system efficiency, ensuring comfort, conserving energy, and protecting the environment. By identifying these issues before they escalate, homeowners can avoid expensive repairs and contribute to a more sustainable future. This proactive approach fosters peace of mind, knowing that their AC system is functioning properly and that they are being responsible stewards of the environment.
Evaluation of Electrical Components
The evaluation of electrical components during an air conditioning (AC) inspection is a critical aspect of maintaining an efficient and safe HVAC system. This evaluation typically includes checking various electrical connections, ensuring proper voltage and amperage levels, and inspecting the condition of wiring and electrical components such as capacitors, contactors, and relays. Any faults found during this inspection can signal underlying issues that may escalate into more significant problems if left unaddressed.
One key area of focus is the integrity of the electrical connections. Loose or corroded connections can lead to inefficient operation of the AC system, increase energy consumption, and even pose safety hazards such as electrical fires. Additionally, evaluating the performance of components like capacitors and contactors is essential; these components are integral to the starting and operation of the compressor and fans. A failing capacitor, for instance, can prevent the system from starting or cause it to run inconsistently, leading to wear on other parts of the system.
Another significant concern is the age and condition of the wiring. Old, frayed, or damaged wires can result in shorts or other safety issues. An inspector will look for signs of overheating, such as discoloration or melted insulation, which could indicate that electrical components are working harder than they should be or that there is an overload issue. This assessment not only helps identify potential future problems but also contributes to the overall safety and reliability of the AC system.
Finally, inspecting the electrical components allows for the identification of inefficiencies that could lead to higher energy bills over time. Identifying and remedying these inefficiencies, such as replacing old components with newer, more efficient models, can enhance system performance, lower operational costs, and prolong the lifespan of the air conditioning unit. Thus, regular evaluations of electrical components are an essential preventive measure in maintaining an AC system and avoiding costly repairs or replacements in the future.
Assessment of Ductwork Integrity
The assessment of ductwork integrity is a critical component of an air conditioning (AC) inspection, as it can significantly affect the efficiency and performance of an HVAC system. Ductwork is responsible for distributing conditioned air throughout a building, and any leaks, blockages, or deteriorations can lead to substantial inefficiencies. During an AC inspection, trained professionals evaluate the ductwork for both physical and functional integrity. This includes checking for obstructions, assessing the material condition, and ensuring that connections are secure. A thorough inspection helps maintain optimal airflow and energy efficiency.
Identifying issues with ductwork can prevent potential future problems that may arise from neglected maintenance. For example, leaks in the ducts can lead to significant energy loss, meaning that the system has to work harder to maintain the desired temperature. This not only impacts energy bills but can also lead to system overuse, increasing wear and tear on components, and potentially resulting in premature failure. Moreover, improperly sealed or insulated ducts can allow contaminants from unconditioned spaces to enter the airflow, degrading indoor air quality and posing health risks to occupants.
An assessment also entails examining the ducts for proper sizing and routing, which are crucial for efficient airflow. Inadequately sized ducts can lead to poor air distribution, hotspots, or cold spots within a building. An inspector may recommend modifications or upgrades to improve duct performance, which can enhance the overall efficiency of the HVAC system and prolong its lifespan. By addressing these issues during an inspection, homeowners can make informed decisions about necessary repairs or upgrades, ensuring a comfortable and safe indoor environment while optimizing energy usage.
In summary, assessing ductwork integrity is an essential aspect of AC inspections that can reveal potential future problems. By identifying leaks, blockages, or structural issues early on, homeowners can take proactive measures to repair and maintain their HVAC systems, leading to improved efficiency, lower energy costs, and enhanced air quality. This proactive approach not only preserves the effectiveness of the AC system but also contributes to a healthier living environment.
Analysis of System Performance Metrics
Analyzing system performance metrics is a critical aspect of air conditioning (AC) inspections, as it provides essential insights into the overall efficiency and functionality of the HVAC system. Performance metrics include a range of data points such as the temperature differential across the evaporator coil, energy consumption rates, airflow measurements, and other operational benchmarks. By closely examining these metrics, technicians can identify any discrepancies from typical performance standards, aiding in the early detection of potential issues that could lead to more significant problems in the future.
One of the primary benefits of evaluating system performance metrics is the ability to spot inefficiencies early on. For instance, if the temperature differential is not within the expected range, it might indicate that the system is struggling to achieve the desired cooling effect, which could be a sign of refrigerant issues, airflow blockages, or mechanical failures such as a failing compressor. Addressing these issues early can prevent more severe breakdowns and costly repairs down the line. Additionally, monitoring energy consumption can help homeowners recognize spikes that could suggest that their system is working harder than necessary, which could be a sign of underlying problems, such as poor insulation or a failing component.
Moreover, a thorough analysis of performance metrics often involves looking at historical data. Understanding how performance has changed over time can reveal patterns that help predict future breakdowns or inefficiencies. For example, if energy usage has gradually increased over several seasons without changes in usage patterns, it may indicate that the system is losing efficiency, prompting a closer inspection and potentially an early intervention.
In summary, by incorporating a comprehensive analysis of system performance metrics into regular AC inspections, HVAC professionals can proactively identify potential future problems. This not only extends the lifespan of the AC unit but also ensures a comfortable living environment and reduces the likelihood of emergency repairs. Regular evaluation of these metrics should be a fundamental part of any maintenance routine, prioritizing both cost savings and system reliability for homeowners.
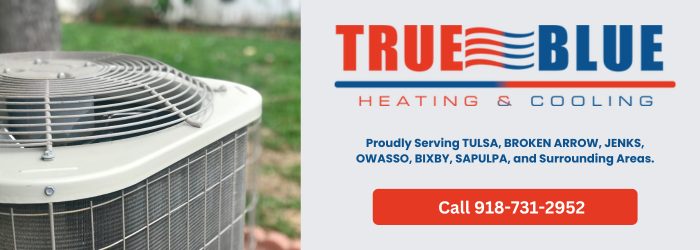
Inspection of Drainage and Moisture Issues
One of the critical aspects of air conditioning (AC) system maintenance is the inspection of drainage and moisture issues. Proper drainage is essential for the efficient operation of an AC unit, as it prevents excess water buildup that can lead to significant problems. The AC system generates condensation as it cools the air, which is then collected in a drip pan and channeled away through a drainage line. If this drainage system becomes clogged, damaged, or misdirected, it can result in moisture accumulation that not only affects the AC unit’s performance but can also lead to other serious issues.
Moisture issues can foster the growth of mold and mildew, which can compromise indoor air quality and pose health risks to occupants. Constructive inspection protocols involve checking drainage pans for cracks, verifying that the drainage line is devoid of blockages, and ensuring that the system is discharging condensation appropriately. Routine inspections often reveal early warning signs of drainage problems, such as standing water or moisture stains around the AC unit, allowing homeowners to address these issues before they escalate into more significant concerns.
Furthermore, AC inspections can help identify potential future problems by assessing the overall state of the drainage system. For example, irregularities in drainage might indicate underlying issues with the AC system’s refrigerant levels or improper functioning of components, which, if left unchecked, could lead to compressor failure or inefficient cooling. By recognizing these indicators during regular maintenance, homeowners can prevent costly repairs and ensure their HVAC systems operate effectively. Additionally, a thorough investigation of drainage and moisture issues during AC inspections contributes significantly to the longevity of the equipment, safeguarding the investment in the AC unit and enhancing overall comfort within the home.